In the laboratories of the Politecnico di Torino, snorkeling masks become respirators.
Creativity, 3D printing, and above all the desire to do something useful to help those who fight on the front line against the pandemic. Thus, in a few days, the Charlotte valves project was born from a Brianza start-up, capable of transforming the full face snorkeling masks of a well-known brand of clothing and sports equipment into emergency respiratory masks. An initiative that also reaches the Politecnico, thanks to the commitment of Alessandro Ferraris, a young research fellow of the Department of Mechanical and Aerospace Engineering (DIMEAS) and the availability of the IAM@PoliTo Interdepartmental Center, who immediately accepted the idea of using their own printers for additive manufacturing to make the valves.
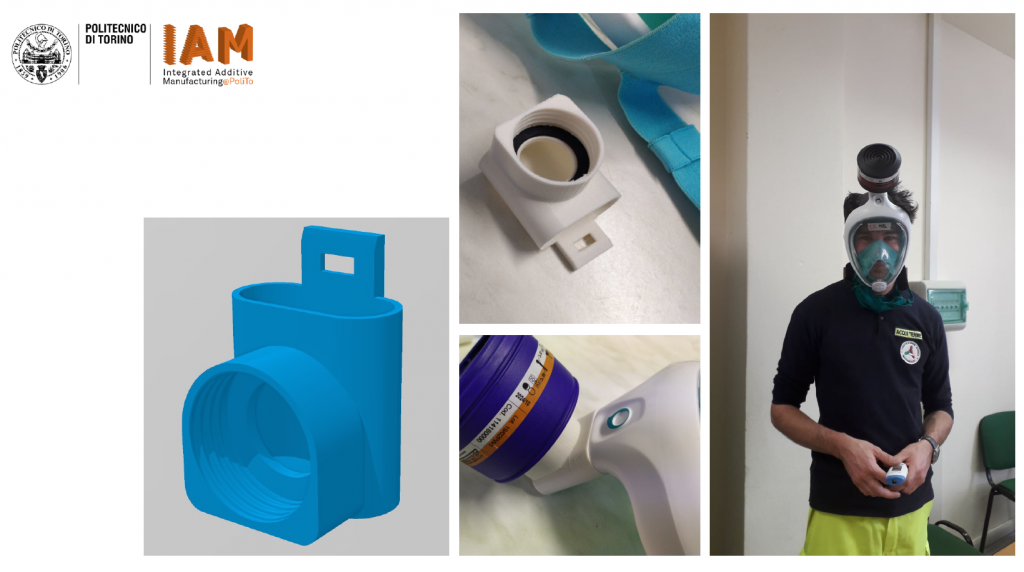
A face shield designed for 3D Printing
A face shield support for medics and professionals designed for 3D Printing by Flaviana Calignano and Giovanni Marchiandi: lightweight structure (less than half of the original); one part and no need for post-manufacturing assembly; Two adjustable headbands that distribute the shield weight and improve comfort when it must be worn all-day; biocompatible material PA12-Nylon; flexible material thanks to the thin part thickness (ONLY 0.8mm); The power of good design for additive manufacturing and a strong collaboration between Prof. Luca Iuliano, Prof. Enrico Macii and Dott. Aprà Franco – Medicina e Chirurgia d’Accettazione e Urgenza – MeCAU – Ospedale San Giovanni Bosco, and Gianvito Urgese. Ready to be printed, 200 parts will be soon ready for people at the Ospedale San Giovanni Bosco, Torino, thanks to Eng. Nunzio Di Bartolo and Eng. Roberta Sampieri FCA – Fiat Chrysler Automobiles. Designed and prototyped at Integrated Additive Manufacturing Center (IAM@PoliTo) at Politecnico di Torino, Department of Management and Production Engineering (DIGEP)
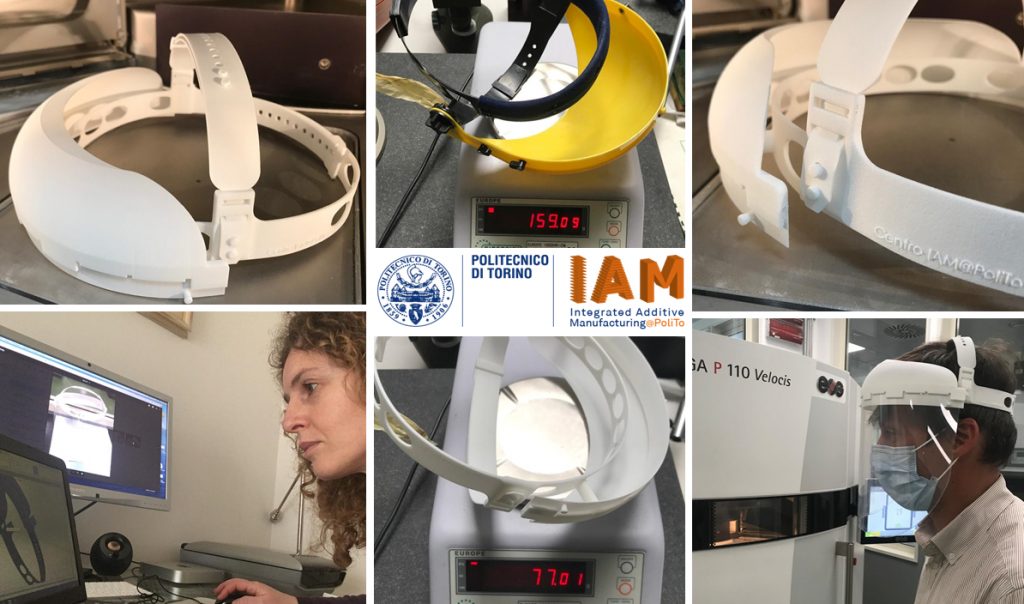